Digitalization creates overview - and surplus
With a software solution from Scanvaegt, the Danish processing company Varde Laks has acquired a comprehensive overview of raw material reception, production, packing, and storage. This means fewer mistakes in the order flow, a higher level of traceability, and Varde Laks can now determine the exact cost price per kg of produced unit.
Varde Laks has succeeded in exporting processed salmon. The turnover has surged forward in the last ten years, leading to an increased number of employees, more tons of raw materials, and most importantly, a substantial need to know all the key data.
The processing company now has this in the form of an upgraded ScanPlant software solution, which was implemented last year. The first version was implemented back in 2014. The new development is that the company’s ERP system, Business Central, from May 2022 has been integrated into the new ScanPlant version.
Valid data and precise cost prices
The software solution is a MES system developed in ScanPlant NG, a complete factory system that monitors production development, stock development, and yield, among other things. The factory system digitizes tasks and creates transparency in various parameters, collectively ensuring optimized operation. The upgraded software solution is developed by Accuratech, partially owned by Scanvaegt Systems.
Lea Schäfer, CFO and IT manager at Varde Laks talks about their experiences with ScanPlant NG MES; "It's somewhat of a dream for us that we have gotten control of all our data. Now, it has become much easier to plan our production based on the raw materials we have. And we can precisely calculate what our cost price is per produced unit and thus adjust the prices for the customers. We couldn't do that before. We have acquired valid data in several areas where we previously just had an uncertain feeling of how things were going".
200 tons of Norwegian salmon per week
Varde Laks employs 45 people at the company, which is currently expanding with new storage facilities across the street. 99 percent of the fish received are salmon raised in Norway. They are delivered by truck in styrofoam boxes packed with ice and five to six fresh salmon in each box. During the high season, it amounts to 200 tons per week. The majority (70-75 percent) is filleted, smoked, sliced, vacuum-packed, and sold for export (90 percent). The largest customer group is hotel and restaurant chains in Europe.
Complete traceability at all stages
When the fish is received at Varde Laks in Denmark, the shipment is given a lot number, which follows the shipment throughout the various processes in the factory.
This ensures complete traceability at all stages through production - there is full control of how the salmon is processed, which spices and packaging have been used, and who the salmon is sold to, according to Lea Schäffer.
All processes are compiled into a report with valid data for documentation.
"We have achieved full data registration of traceability across our entire production, and it is extremely important for our approach to food safety," says Lea Schäffer, continuing:
"Previously, when preparing a traceability test for the Food Administration, we had to collect data manually, and it could easily take three to four hours. We ran back and forth from the office to the production, and many mistakes were made. Now we have the exact data in our system and can provide them in about 20 minutes."
Profitability has increased
The ScanPlant software also provides a good overview of the ingredients and parts needed in production - it could be salt, herbs, and packaging. The overview also applies to inventory management.
The integration with Business Central means that packing is done directly against orders and that data from the finished packed orders are automatically transferred from the packing department for invoicing.
"With the overview we have gained of the various processes, we save at least two to three people's work in the office. In addition, we have minimized our give-away, so we have definitely become more profitable," points out Lea Schäffer.
"But it also has a significant impact that everyone has gained understanding and respect for the data we work with, which now forms the basis for the business decisions we make," adds Lea Schäffer, who also praises the cooperation with the development department at Accuratech in Holstebro, Denmark:
"We have a fantastic collaboration with Accuratech, who have strong knowledge in the food industry. They understand what solutions I want and solve the issues I present to them."
Â
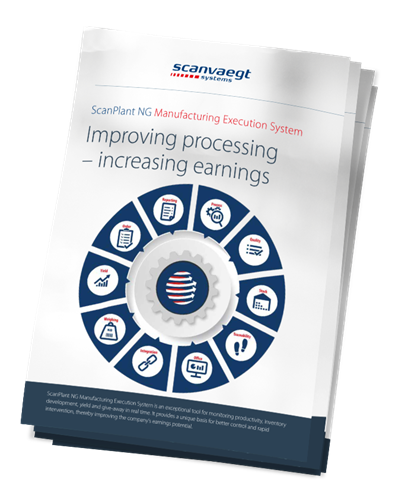
Read brochure
ScanPlant NG MES
Do you have questions or do you want us to call you?
Then send us an email – we are ready to assist you Â